What is French Polishing?
French Polishing is a technique that has been around since the 1600s, where a natural resin called shellac is applied to wood in thin layers.
This results in a glossy finish that enhances the wood’s beauty and grain.This technique involves dissolving flake shellac in denatured alcohol and then applying it to the wood with a pad made of cotton wool.
It was popular among furniture and musical instrument makers in the 18th and 19th centuries. However, its popularity declined in the 20th century due to the development of synthetic finishing materials.
French Polishing produces a finish with depth and lustre that merges with the wood, providing a protective and aesthetically enriching finish.
LS Surface Repairs uses this traditional technique and combines it with modern advancements to ensure it remains relevant in today’s world, particularly in the care and restoration of antique musical instruments.
So, whether you have a cherished family heirloom or a newly acquired antique instrument that requires attention, consider the benefits of French Polishing for a long-lasting and beautiful finish.
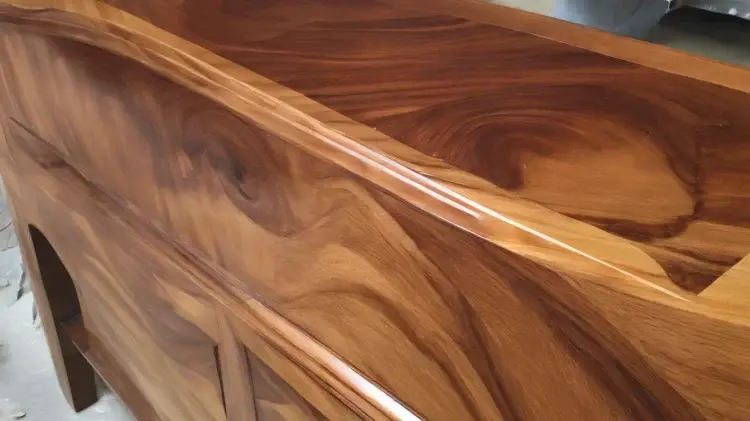
French Polishing Process
Our French Polishing process at LS Surface Repairs is a mark of our commitment to exquisite craftsmanship and keen attention to detail.
Here is a concise, step-by-step outline of how we bring this centuries-old art to life on your treasured furniture:
Preparation
Preparation of the surface to be polished is extremely important and to achieve the best results it is necessary to remove any slight imperfections that may not be noticeable under a varnish or wax finish. This may involve stripping off an old varnish with fine wood stripper or removing a wax or oil with aa wax and polish remover.
Once stripped you will then need to rub the surface down with fine abrasive paper to obtain a smooth finish.
If the wood is open grained and a mirror like finish is required, the grain should be filled using a suitable grain filler. Alternatively, extra coats of polish may be applied and then cut back between coats with ultra fine steel wool until the grain has been filled.
Initial Shellac Application
A thin coat of shellac is applied to the unencumbered wood. This initial layer serves as a sealer, preparing the surface for further polishing. Once it has dried, it is delicately sanded with fine-grade sandpaper to create a perfectly smooth foundation.
Making a French Polishing Rubber
The “dabber” or “rubber” is a crucial instrument in French Polishing that is custom-made by wrapping lint-free cotton cloths with cotton wadding. The size of the rubber can vary according to the user or the size of the job to be completed.
Applying the French Polish
Load the rubber by pouring the French polish directly onto the cotton wadding. Do not pour the polish directly onto the face of the rubber.
The first few layers function as a sealant, and the dabber is moved along the grain of the wood to guarantee even coverage. This step is essential in establishing the groundwork for the glossy finish.
Building up Layers
After allowing the polish to harden briefly, further applications are made by using the rubber in a circular and figure-of-eight motion.
The final pass in the sequence goes with the grain, passing fairly quickly and lightly over the surface. Always finish the sequence along the grain.
Spiriting Off
Once a sufficient layer has been achieved on the surface, spiriting off can commence to produce the final high-gloss finish. A new rubber with French polish that has been thinned down with methylated spirit.
Approximate ratio: two parts French Polish to one part methylated spirit.
Apply this polish as before in a circular or figure-of-eight motion and again finish by going along the grain.
Finally, pour a small amount of methylated spirit and a small amount of French polish and rub this up and down the work to remove any high spots. Move the rubber lightly and quickly over the surface to achieve a gloss finish.
Burnishing
A French polish finish does not have to be a high-gloss mirror finish every time. Sometimes a softer level of sheen is required.
To achieve this, all you have to do is to allow the polished surface to harden for a few days then cut back the polish using ultra-fine steel wool to remove any imperfections. Finally, finish with a coat of Wax Polish.
For a mirror finish, you need to leave the French polish to fully harden for about a week to ten days, then cut the surface back with ultra-fine steel wool and remove any dust with a tack cloth.
Next, apply burnishing cream with a clean cotton cloth, polishing vigorously and occasionally turning the cloth until the deep mirror finish is achieved.
Throughout this process, LS Surface Repairs pays meticulous attention to every detail, ensuring that every step is executed with precision.
How Can We Help – From Homes to Offices to Hotels
- Furniture: From antique dining tables and chairs to elegant cabinets and wardrobes, our French Polishing breathes new life into these pieces, highlighting their natural beauty and intricate details.
- Staircases and Bannisters: Transforming these often-overlooked parts of a home into stunning features with a rich, glossy finish that accentuates the wood’s character.
- Office Furniture: We extend our services to office furniture such as desks, conference and boardroom tables, and wooden fixtures, ensuring elegance in professional spaces.
- Decorative Wood: Including door frames, coffee tables, television cabinets, and even wooden stools, each can benefit from the enhanced depth and durability French Polishing offers.
At LS Surface Repairs, we are committed to preserving and enhancing the natural elegance of wooden items through the art of French Polishing.
Whether it’s a bedside cabinet and a executive boardroom table, our craftsmanship ensures that each item reflects its inherent beauty and carries a finish of the highest quality.